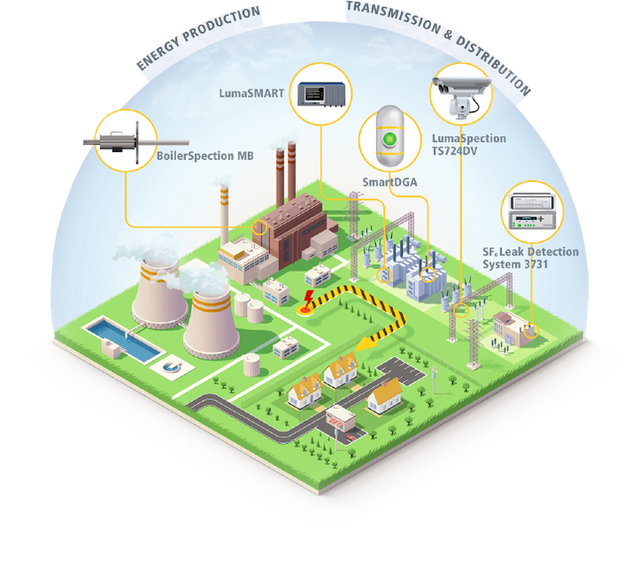
Global Energy
Usage Will Grow
The electric grid is the vast network of transmission lines, substations and power plants that deliver electric power to our homes and businesses. It is one of the great engineering feats of the 20th century.
But the current grid is inefficient, and has changed little in concept since the days of Thomas Edison. Up to ten percent of the power we generate is lost in transmission.
A “smart” electric grid allows homes and businesses to use, as well as produce and sell, electricity in a more technologically advanced way.
Investment will be needed in asset monitoring for new and existing transformers and load tap changers and for this purposes LumaSense Technologies offers sophisticated solutions.
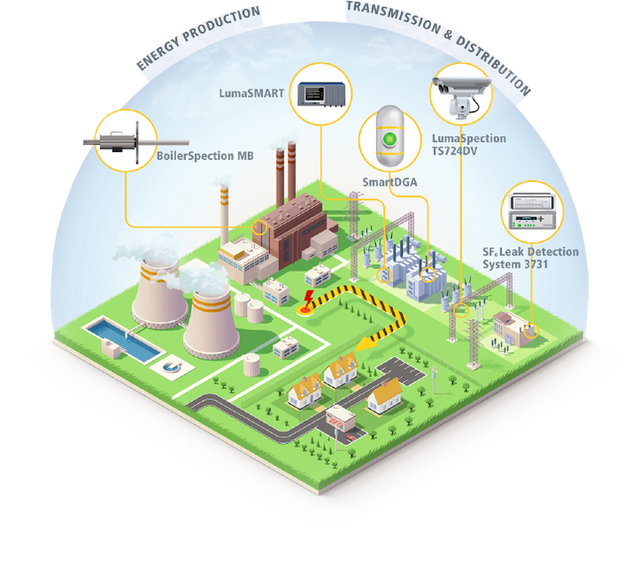
Global Energy
Usage Will Grow
The electric grid is the vast network of transmission lines, substations and power plants that deliver electric power to our homes and businesses. It is one of the great engineering feats of the 20th century.
But the current grid is inefficient, and has changed little in concept since the days of Thomas Edison. Up to ten percent of the power we generate is lost in transmission.
A “smart” electric grid allows homes and businesses to use, as well as produce and sell, electricity in a more technologically advanced way.
Investment will be needed in asset monitoring for new and existing transformers and load tap changers and for this purposes LumaSense Technologies offers sophisticated solutions.
Boiler Spection MB
The BoilerSpection MB system is an easy-to-use mobile imaging solution that can be used for boilers and furnaces. This portable unit includes all the components necessary to record images in only minutes. Armed with this information, operators can then direct cleaning operations, regulate flow of fuel and air, reduce emissions, reduce fuel consumption, and speed boiler start up processes.
Boiler and Furnace Combustion Imaging
The challenge every coal plant owner or operator faces is to generate the maximum amount of energy with the lowest emissions in the safest and most economical way. Scale or slag buildup on platens and tubes results in inefficient heat transfer and can also damage the tubes.
Currently, coal plant operators use a number of ways to clean boiler tubes, but have inadequate methods to measure their effectiveness. Many of these methods have negative impacts such as prolonged downtime and thermal stress to the boiler tubes.
Our Solution
BoilerSpection is a revolutionary thermal imaging system with the ability to see through flames that helps coal plants run more efficiently, extract more energy from their coal, and increase productivity.
With BoilerSpection, coal plant operators can proactively manage their boilers by gaining visibility on scale buildup directly on the boiler tubes. The number of cleaning cycles and downpower operations can be minimized resulting in increased operating efficiency and reduced mechanical stress that can lead to tube failure. Return on investment (ROI) studies by customers have found ROIs measured in only a few months, not years.
Boiler Spection MB
The BoilerSpection MB system is an easy-to-use mobile imaging solution that can be used for boilers and furnaces. This portable unit includes all the components necessary to record images in only minutes. Armed with this information, operators can then direct cleaning operations, regulate flow of fuel and air, reduce emissions, reduce fuel consumption, and speed boiler start up processes.
Boiler and Furnace Combustion Imaging
The challenge every coal plant owner or operator faces is to generate the maximum amount of energy with the lowest emissions in the safest and most economical way. Scale or slag buildup on platens and tubes results in inefficient heat transfer and can also damage the tubes.
Currently, coal plant operators use a number of ways to clean boiler tubes, but have inadequate methods to measure their effectiveness. Many of these methods have negative impacts such as prolonged downtime and thermal stress to the boiler tubes.
Our Solution
BoilerSpection is a revolutionary thermal imaging system with the ability to see through flames that helps coal plants run more efficiently, extract more energy from their coal, and increase productivity.
With BoilerSpection, coal plant operators can proactively manage their boilers by gaining visibility on scale buildup directly on the boiler tubes. The number of cleaning cycles and downpower operations can be minimized resulting in increased operating efficiency and reduced mechanical stress that can lead to tube failure. Return on investment (ROI) studies by customers have found ROIs measured in only a few months, not years.
LumaSMART
Fluoroptic-based temperature monitoring solution and probe system that provides accurate, real-time temperature readings for winding hot spots in EHV/UHV/HVDC transformers, large power transformers and reactors.
Winding Hot
Spot Monitoring
As transformers are often operated on overload condition, monitoring the transformer winding hot spot is critical to safeguard this asset from damage and extend its usage. Complex temperatures and harsh environments, such as high voltage and RFI and EMI emissions make accurately measuring hot spot winding temperature in transformers difficult.
Hot spots are the highest temperature area in the transformer based on flux leakage from the windings and can degrade the insulating paper making the transformer susceptible to failure. Since transformer life is dependent on the insulating paper, accurately monitoring over temperature conditions is critical.
Conventional methods simulate or calculate this temperature, but they can inaccurately show up to 20 °C difference from the actual hot spot temperature. It has been shown that top oil has significant time lag related to winding real temperatures. Because transformer aging rate doubles for every 6 °C over temperature set point, inaccurate temperature measurements can lead to transformer damage and transformer loss of life.
Our Solution
Fiber optic monitoring enables true “hot spot” measurement by sensing temperature directly in the windings. Winding Temperature Indicators “infer” hot spot measurement by measuring top or bottom oil temperature which significantly lags the real hot spot.
LumaSense Technologies’ brand LUXTRON pioneered the field of fiber optic winding temperature measurement more than 25 years ago and today is a premier provider of direct, real time hotspot monitoring and control systems for the power utility industry.
LumaSMART
Fluoroptic-based temperature monitoring solution and probe system that provides accurate, real-time temperature readings for winding hot spots in EHV/UHV/HVDC transformers, large power transformers and reactors.
Winding Hot
Spot Monitoring
As transformers are often operated on overload condition, monitoring the transformer winding hot spot is critical to safeguard this asset from damage and extend its usage. Complex temperatures and harsh environments, such as high voltage and RFI and EMI emissions make accurately measuring hot spot winding temperature in transformers difficult.
Hot spots are the highest temperature area in the transformer based on flux leakage from the windings and can degrade the insulating paper making the transformer susceptible to failure. Since transformer life is dependent on the insulating paper, accurately monitoring over temperature conditions is critical.
Conventional methods simulate or calculate this temperature, but they can inaccurately show up to 20 °C difference from the actual hot spot temperature. It has been shown that top oil has significant time lag related to winding real temperatures. Because transformer aging rate doubles for every 6 °C over temperature set point, inaccurate temperature measurements can lead to transformer damage and transformer loss of life.
Our Solution
Fiber optic monitoring enables true “hot spot” measurement by sensing temperature directly in the windings. Winding Temperature Indicators “infer” hot spot measurement by measuring top or bottom oil temperature which significantly lags the real hot spot.
LumaSense Technologies’ brand LUXTRON pioneered the field of fiber optic winding temperature measurement more than 25 years ago and today is a premier provider of direct, real time hotspot monitoring and control systems for the power utility industry.
SmartDGA
for Transformers
Over time, as thermal and electrical stresses accumulate, the transformer’s insulating materials start to breakdown and release different gases. Detect these gases in transformer insulating oil by using sensitive and reliable Dissolved Gas Analysis (DGA) techniques to determine the type of impending or occurring fault.
LumaSense offers a cost-effective online monitoring solution for LTCs and transformers based on proven non-dispersive infrared (NDIR) technology. With online monitoring, utilities can automate the manual oil sample process to capture data every day and implement condition based maintenance (CBM) strategies to reduce the number and frequency of maintenance cycles.
Our Solution
The SmartDGA instrument works in cycles (as often as every 4 hours) to obtain a sample of oil, detect concentrations (in PPM) of key gases, and record the values. The robust DGA Viewer software includes industry recommended tools such as rates, ratios, Duval Triangle for detecting fault types, including Partial Discharge (PD), Discharges of Low Energy (D1), Discharges of High Energy (D2), Thermal Fault (T1), Thermal Fault (T2), and Thermal Fault (T3).
The LumaSense SmartDGA family represents the industry’s most cost-effective Dissolved Gas Analysis solution, designed to provide the best user experience and maximum flexibility.
The SmartDGA Guide™ instrument provides comprehensive online DGA results that enable diagnostic techniques. The instrument uses NDIR technology to measure and record all nine industry recommended fault gases Acetylene (C2H2), Ethane (C2H6), Ethylene (C2H4), Carbon Dioxide (CO2), Carbon Monoxide (CO), Hydrogen (H2), Methane (CH4), Nitrogen (N2), Oxygen (O2), and Moisture found in insulating oil.
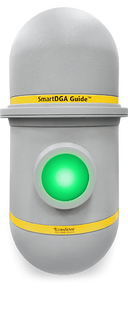
SmartDGA
for Transformers
Over time, as thermal and electrical stresses accumulate, the transformer’s insulating materials start to breakdown and release different gases. Detect these gases in transformer insulating oil by using sensitive and reliable Dissolved Gas Analysis (DGA) techniques to determine the type of impending or occurring fault.
LumaSense offers a cost-effective online monitoring solution for LTCs and transformers based on proven non-dispersive infrared (NDIR) technology. With online monitoring, utilities can automate the manual oil sample process to capture data every day and implement condition based maintenance (CBM) strategies to reduce the number and frequency of maintenance cycles.
Our Solution
The SmartDGA instrument works in cycles (as often as every 4 hours) to obtain a sample of oil, detect concentrations (in PPM) of key gases, and record the values. The robust DGA Viewer software includes industry recommended tools such as rates, ratios, Duval Triangle for detecting fault types, including Partial Discharge (PD), Discharges of Low Energy (D1), Discharges of High Energy (D2), Thermal Fault (T1), Thermal Fault (T2), and Thermal Fault (T3).
The LumaSense SmartDGA family represents the industry’s most cost-effective Dissolved Gas Analysis solution, designed to provide the best user experience and maximum flexibility.
The SmartDGA Guide™ instrument provides comprehensive online DGA results that enable diagnostic techniques. The instrument uses NDIR technology to measure and record all nine industry recommended fault gases Acetylene (C2H2), Ethane (C2H6), Ethylene (C2H4), Carbon Dioxide (CO2), Carbon Monoxide (CO), Hydrogen (H2), Methane (CH4), Nitrogen (N2), Oxygen (O2), and Moisture found in insulating oil.
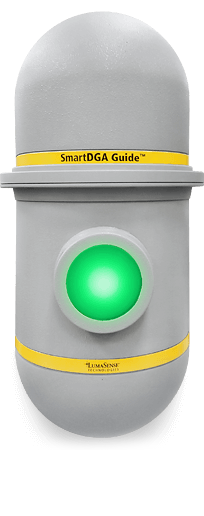
LumaSpection
TS724DV
AUTOMATED & REMOTE
THERMAL IMAGING
Increasing reliability through continuous and remote substation asset monitoring
For many years portable thermal imaging cameras have been a reliable tool in condition-based and preventive maintenance of electrical distribution systems in low-, medium-, and high-voltage installations, where they are often used at periodic time intervals. Optimized maintenance concepts in this industry however more and more call for the continuous monitoring of critical substation connections and assets, such as transformers, bushings, disconnects and capacitor banks, to provide an automated early-warning detection of developing failures.
Our Solution
ThermalSpection™ 724DV - An Automated, Continuous Thermal and Visual Imaging system to Identify Thermal Abnormalities within Electrical Power Substations.
(two images at the bottom).
The ThermalSpection™ 724DV monitoring system can combine multiple devices, including pan and tilt cameras, fixed cameras, and pyrometer for the most cost effective and comprehensive system solution for electric power substations.
Designed with advanced maintenance-free electronics and industrial protective packaging, the ThermalSpection™ 724DV system offers a high degree of accuracy for demanding electric power utility’s while accurately measuring asset temperature without contact in even the most adverse environments. The system includes software that controls, captures and stores fully radiometric (thermal) images continuously into an SQL archive that supports alerts and retrospective analysis.
(upper image on the right side).
LumaSpection
TS724DV
AUTOMATED & REMOTE
THERMAL IMAGING
Increasing reliability through continuous and remote substation asset monitoring
For many years portable thermal imaging cameras have been a reliable tool in condition-based and preventive maintenance of electrical distribution systems in low-, medium-, and high-voltage installations, where they are often used at periodic time intervals. Optimized maintenance concepts in this industry however more and more call for the continuous monitoring of critical substation connections and assets, such as transformers, bushings, disconnects and capacitor banks, to provide an automated early-warning detection of developing failures.
Our Solution
ThermalSpection™ 724DV - An Automated, Continuous Thermal and Visual Imaging system to Identify Thermal Abnormalities within Electrical Power Substations.
(two images at the bottom).
The ThermalSpection™ 724DV monitoring system can combine multiple devices, including pan and tilt cameras, fixed cameras, and pyrometer for the most cost effective and comprehensive system solution for electric power substations.
Designed with advanced maintenance-free electronics and industrial protective packaging, the ThermalSpection™ 724DV system offers a high degree of accuracy for demanding electric power utility’s while accurately measuring asset temperature without contact in even the most adverse environments. The system includes software that controls, captures and stores fully radiometric (thermal) images continuously into an SQL archive that supports alerts and retrospective analysis.
(upper image on the right side).
SF6 Leak Detection in Enclosed GIS Substations
Direct leak detection in
enclosed GIS substations require highly sensitive and reliable SF6 gas detection.
High-voltage SF6-insulated switchgears require specific monitoring and operation & maintenance procedures to prevent and limit the emissions of the insulating gas (SF6 – sulfur hexafluoride), which is a very potent greenhouse gas.
New regulatory frames like the F-Gas Directive (EC 517/2014) are mandating the use of leak detection systems in the vast majority of high-voltage SF6-GIS installation in order to better mitigate the risk of SF6 emissions.
Our Solution
Our Gas Monitors based on Photoacoustic Spectroscopy (PAS) are field-proven in several applications and they were perfected for SF6 leak detection. Our SF6 Leak Detection System – INNOVA 3731 – benefits from this expertise.
With its very low detection limit (6 ppb SF6 in ambient), our INNOVA 3731 system is a direct leak detection solution capable of integral monitoring of large switchgear rooms. It verifies that your SF6-GIS equipment operates below the industrial target of 0.5% yearly leakage rate or better.
With up to 24 different channels, the 3731 system enables an extensive distribution of sampling points over the whole monitored substation in order to maximize the coverage area and minimize the detection response time. Each sampling line (nylon tubing) can be extended up to 75 m.
The detection system has extended self-test routines which maintain the reliability of the results. Besides, our stable PAS design only requires calibration once per year.
SF6 Leak Detection in Enclosed GIS Substations
Direct leak detection in
enclosed GIS substations require highly sensitive and reliable SF6 gas detection.
High-voltage SF6-insulated switchgears require specific monitoring and operation & maintenance procedures to prevent and limit the emissions of the insulating gas (SF6 – sulfur hexafluoride), which is a very potent greenhouse gas.
New regulatory frames like the F-Gas Directive (EC 517/2014) are mandating the use of leak detection systems in the vast majority of high-voltage SF6-GIS installation in order to better mitigate the risk of SF6 emissions.
Our Solution
Our Gas Monitors based on Photoacoustic Spectroscopy (PAS) are field-proven in several applications and they were perfected for SF6 leak detection. Our SF6 Leak Detection System – INNOVA 3731 – benefits from this expertise.
With its very low detection limit (6 ppb SF6 in ambient), our INNOVA 3731 system is a direct leak detection solution capable of integral monitoring of large switchgear rooms. It verifies that your SF6-GIS equipment operates below the industrial target of 0.5% yearly leakage rate or better.
With up to 24 different channels, the 3731 system enables an extensive distribution of sampling points over the whole monitored substation in order to maximize the coverage area and minimize the detection response time. Each sampling line (nylon tubing) can be extended up to 75 m.
The detection system has extended self-test routines which maintain the reliability of the results. Besides, our stable PAS design only requires calibration once per year.